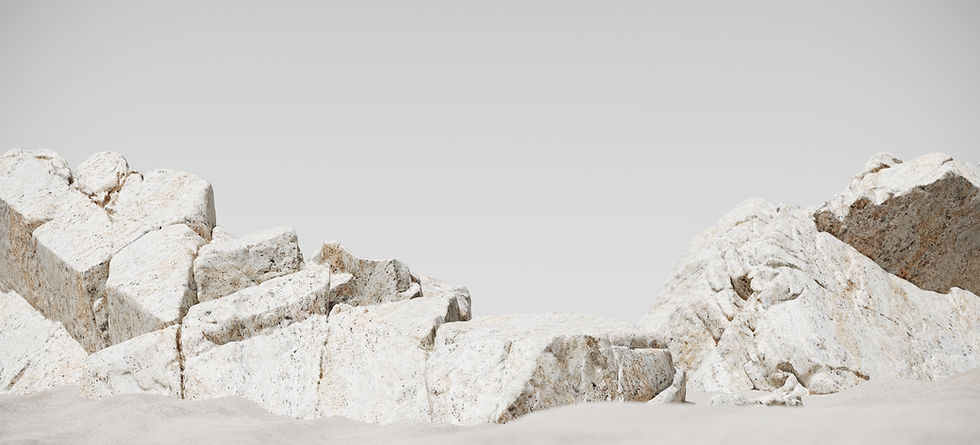
GM.SI Series
The GM.SI Series X-ray orientation systems are heavy duty production units especially designed for locating the flat or notch position on all kinds of single crystals, from the smallest to the largest size. All single crystal can be processed, for all applications such as semiconductors, opto-electronics, optics, etc.
â– Orientation processes
-
Flat & Notch on "as grown" ingots
-
Flat & Notch on ground ingots (cylindrical)
â– Orientation measurements
-
Ingot flat
-
Ingot notch
-
Seed axis (round or square seeds, with optional holder)
-
Wafer face
-
Wfaer flat (optional holder)
■Performance​
-
X-ray detection : ± 0.01°
-
Orientation process : ± 0.03 to 0.05°, depending of configuration and crystals.
-
Measurements : ± 0.01° to 0.03°

Configurations
The GM.SI-…-R type X-ray orien- tation systems are specific models of our GM.SI series X-ray units, specifically designed for operation in combination with grinding equipment where the ingot is hold between centers, and the grinder spindle equipped with rotation control and display.
Like all models of the GM.SI series, the GM.SI-…-/R models are available as a single station unit or in dual-station mixed configurations.
This can be in combination with either a GM or a GM.WS series work station.
Goniometer
An extremely robust goniometer assembly supports the complete ingot handling mechanism. The goniometer shaft incorporates a specimen holder which is used as a reference plane for easy calibration of the equipment, measuring wafer orientation and for mounting optional holders.
A reference roller having its edge in the same plane as the holder is mounted directly on the shaft.
Goniometer / detector rotation range : <0° to ca. 100°
Capacities
GM.SI models are available in several capacities which are configured according to the user's requirements. They cover a complete range of applications from diameter 2-inch up to 200 mm and 800 mm in length.
A dedicated model is available for ingots of diameter 300 mm.
(specific documentation on request)
Angle reading
Digital angle display in decimal degrees (0.01°), in deg. min. sec (optional) or through a PC.
Reset to zero at any position
Absolute or relative angle value can be alternatively displayed
Automatic recalibration at start-up or at any time.
Safeties and protections
The equipment has been designed to offer both maximum protection and easy operation.
-
Electromagnetic rotary shutter controlled by a non latching foot switch.
-
Shutter interlock switch actuated by the ingot in measuring position
-
Green / Red control lights : indication of shutter status.
-
"X-ray ON" light with automatic equipment shut-off in case of lamp failure.
-
Shields and screens stop direct or scattered radiation
X-ray generator
-
Output voltage : 30 kV – DC
-
Maximum rating : 30 mA
-
X-ray tube : copper target, water cooled
-
Apparent focus : linear fine focus
-
Mains : 220 V 50/60 Hz, 1-phase, 10 A
-
Water supply : 2.5 bar. Flow rate 3.5 l/min
Detection unit
Proportional counter linked to a special integrator with peak amplifier, giving a high detection accuracy.
Voltage is adjustable from 1000 to 1850 V
Voltmeter and adjustment potentiometer are located in the casing facing the operator
The easiest and most accurate way of grinding a flat or a notch on an ingot at the proper orientation is provided when the same ingot holding and orientation transfer system is used on both the X-ray goniometer and the flat/notch grinder.
Additionally, best results are obtained when the orientation established on the goniometer can be transferred to the grinder simply by setting its spindle rotation angle at a given value. This is achieved when the goniometer is fitted with angular display of the ingot rotation and the grinder with angular display of the spindle rotation.
Ingot holding system
The ingot (fitted with two steel centering pieces) is hold between two ball centers. Up and down motion of the upper center assembly on a rigid column is pneumatically controlled with foot operated switches, thus leaving the hands free.
The above assembly is mounted on a pneumatically controlled sliding work-table which brings and maintains the ingot in contact with the reference roller, regardless of ingot diameter and shape (as grown ingots). The beam focuses at the contact point between ingot and roller.
Ingot rotation
The upper center ball assembly is part of a rotating cylinder which also incorporates a reference pin. The pin is spring loaded. The rotation angle of the cylinder is displayed digitally, in the same way as the goniometer rotation itself.
A pneumatically actuated fine rotation control and brake system enables accurate rotation control of the ingot at any position.
Ingot orientation process
-
Affix a centering piece with slot at the ingot upper end, and a centering piece without slot at the bottom end.
-
Place the ingot between the goniometer ball centers, the reference pin of the upper assembly latching into the slot of the centering piece.
-
Proceed to ingot orientation by rotating the ingot until a reflection peak is obtained. Use the fine rotation control to get an accurate orientation.
Note the value displayed on the "ingot rotation" display.
-
Place the ingot on the grinder, the index pin latched into the slot of the piece.
-
After the ingot OD has been ground, rotate the grinder spindle until its rotation display indicates the same value as the one noted.
-
Proceed to flat or notch grinding, then to the secondary flat when required.

Upper rotating assembly with angle encoder, ball center, latch pin and fine rotation control.


A - GM.SI-…-/R goniometer
B - Grinder with compatible holding
system and rotation angle display
1 - Goniometer angle display
2 - Ingot rotation angle display
3 - Grinder spindle rotation angle display
4 - Lower ingot centering piece
5 - Upper ingot centering piece
Orientation measurements
Ingot Flat & Notch
-
After grinding, the ingot is placed again on the goniometer and the flat or notch checking device brought and maintained in contact against the flat or against the notch of the ingot.
-
The goniometer fine control knob is rotated until a reflection peak is obtained. The goniometer angle readout system directly displays the grinding error.
Wafer flat
-
An easily adaptable dedicated holder is available, which can be placed and removed without the need of resetting or recalibrating the equipment. (See picture below)
Seed axis
-
A dedicated holder is also available, which attaches as described above. (See picture below)

Ingots centering pieces of various sizes (diameter and length) can be supplied to suit specific grinder configurations.
Grinder attachments (ball centers and latch pin assembly) can also be supplied if required.
(See picture on the right)

Ball center with morse conus for grinder. The latch pin attachment mounts on the cylindrical part.
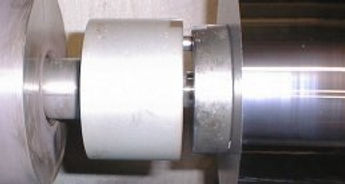
Grinder with ball center and latch pin assembly

Attachment for wafer flat orientation measurement

Seed holder attachment
Delta technologies permanently improves his products.
Equipment may differ from the data mentioned in this non contractual document.